Conventional Pipe Umbrella
The tubular Pipe Umbrella system is capable of increasing stability and safety in the work area, stabilizing not only the region of the cap, but also reflecting on the frontal stability, thereby mitigating the deformations in the rock mass induced by the excavation.
It is an easy-to-implement system, which is one of the main advantages, due to the type and cost of the equipment used in the installation (Drilling Jumbo) and the low specialization of the workers, adapting perfectly to variations in geological conditions.
Description
More Information
In order to reach the lengths specified in the project, the ends of the tubes are machined to allow the splices that can be made through welding or, more commonly, through male-female threads.
Drillings are made along the length of the tubes, which can be at every meter or every 0.50 m at the discretion of the project, with the purpose of installing rubber sleeve valves to carry out the injection of cement lime. As a standard, 04 holes are made in a cross shape in a single section, 5 cm apart, which, when covered by the rubber tube, form the sleeve valve.
Metal rings are welded to both ends of each sleeve valve, which have the function of preventing the valves from moving during the installation of the steel tube in the foundation.
The end of the tube of the first segment to be installed is plugged in the shape of a cone, to facilitate its introduction into the drilling. In some projects, the installation of centralizers in the pipe to be installed is also requested.
At the opposite end, that is, the last segment that makes up the forepoling tube, it will be made of rigid PVC with a thread, with a length of 3.0 m and a diameter similar to that of the metallic tube.
The PVC pipe is located in the cross-over forepoling area, serving to guide the injection shutter and, as it is still installed inside the tunnel excavation section, it is broken to insert the crankshafts one by one until the line is broken (steel) is above the mentioned section.
Thus, this last segment has no “structural” function.
Installation Processes
Drilling
Pre-drilling is done with a hydraulic or pneumatic drilling rig, capable of drilling at any angle and direction, with a minimum torque of 400 Kgf.m and advance force capable of drilling holes fully coated or not. Tricone-type drill bits with a diameter of at least 4 inches are commonly used. Care must be taken to ensure that the holes are made by processes that minimize the change of the natural state of consistency or compactness of the ground. For that, the advance of the drilling tool and the pressure of injected water, as well as the procedures to guarantee the stability or containment of the walls of the hole, must be controlled. The entire drilling process must be monitored and recorded in specific reports that provide the history of the hole, to identify the rock mass traversed, as well as the observed occurrences, such as localized water losses or identified faults or voids.
Pipe installation
At the end of the drilling, the tube is manually transported from the assembly area to the drilling location. The introduction of the tube and its installation must be done slowly, but it continues. Normally, drilling equipment is used to assist in the installation of the pipe, but with discretion, without applying excessive pull-down.
Forepoling injection
The forepoling injection aims at the correct filling of the annular space between the steel tube and the perforation performed, aiming to incorporate/solidify the steel element to the solid for the correct transfer or absorption of loads by the forepoling.
In the case of heavily fractured rock mass, grout injection under low pressure and volume can be an important component in stabilizing blocks and filling fractures, which may also reflect on the reduction of permeability of the rock mass traversed. The first stage of injection or sheath is performed with a simple shutter, through the interior of the forepoling tube, in the first sleeve (bottom).
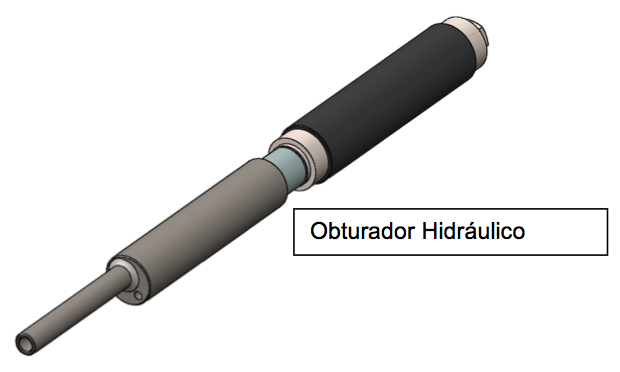
Simple Hydraulic Shutter
Then, after an interval of time between 2 and 3 hours, the cleaning of the inside of the forepoling tube is performed, by introducing a PVC column inside each one of them, promoting the circulation of water to clean the remaining grout from the sheath, essential for the sequence of injections without locking the shutter.
The injection is then continued, sleeve by sleeve, observing a time interval between 8 and 10 hours after sheath application. The new injection phase with controlled pressure and volume, called primary, begins. The primary injection, then, sleeve by sleeve, is performed with controlled volume and pressure, through a double shutter that allows the injection of individual sleeves.
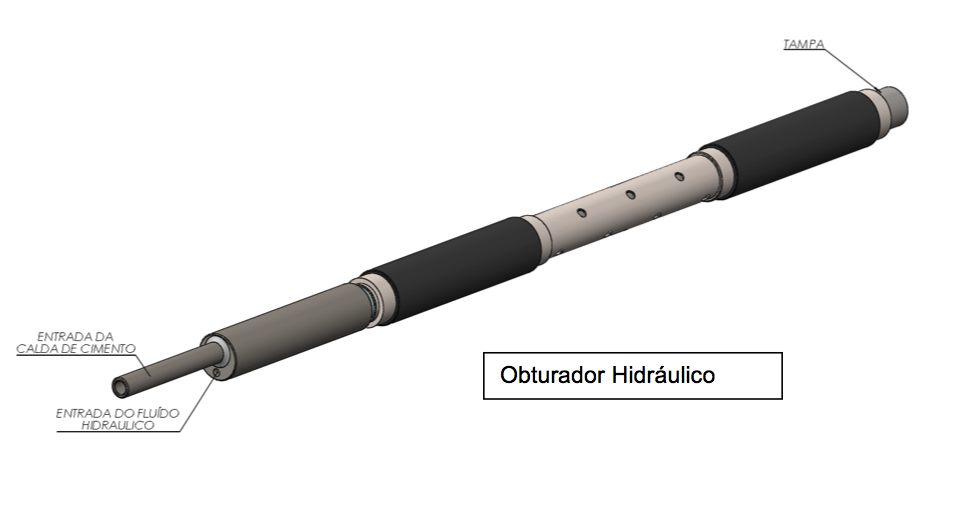
Double Hydraulic Shutter